Software
Introduction
Complex ASICs with multiple operational conditions demand for the automatization of the testing environment to cope with the extensive measurements, complete characterization of the ASIC and post calibration procedure.
Sub-systems as phase arrays and core ICs require fine phase control over 3600 range at multiple amplitude conditions to define gain and window function. Phase and amplitude measurements should be carried out for each channel, frequency of operation and temperature conditions.
The table below outlines a possible testing requirement for a quad-core ASIC for phase arrays. In the example below the total number of measurements for complete characterization of the core IC is 61400. Such large number of measurement conditions demand a comprehensive automatization procedure. Furthermore, post-processing error correction is required to reduce the phase and amplitude variations which directly impact on the scanning angle and side lobes.
Parameter | Value | Comment |
Phase steps | 128 | |
Amplitude steps | 8 | |
Channel | 4 | Quad-core ASIC |
Frequencies | 5 | Multiple bands |
Temperature | 3 | Low/Norm/High Temperature |
Total number of mesurements | 61400 | TX |
Solution
The simplicity of the automatization solution derives from the use of a single platform for automatization and post-processing evaluation procedures.
The solution enables multiple hardware control modes for directly monitoring the main signals of the platform.
The development environment is based on Python language, eliminating the need to run multiple scripts and software platforms to determine the error vectors to perform post-measurement calibration and analysis.
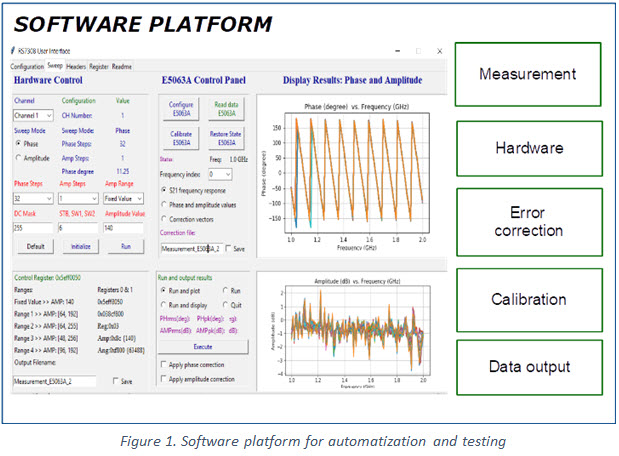
Main Features
- Hardware control (USB or UART)
- Measurement control
- Output data (s2p and ASCII)
- Calibration
User Interface
- Hardware control
- Phase and amplitude sweeps
- DC current readings
- Easy error correction procedure
System Integration
The software platform enables direct evaluation of the sub-system from the post processing results. An example of the evaluation of an array with (blue) and without (red) error correction at scanning angle of -150. Without error correction, the side lobe levels raised by approximately 10 dBs. Such system analysis is obtained directly from characterization and evaluation platform, facilitation the verification and analysis of the sub-system prior to its final implementation.
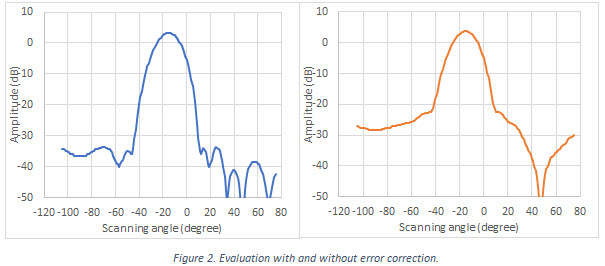
Customization
RIO SYSTEMS offers customization of the solution to customers to meet the requirements of different development environment. The customization of the platform can be done at the following levels
- Hardware level – Customization of the control interface to any user defined ASIC
- Measurement level – Customization of the solution to support any user defined measurement equipment
Inquiring and information
For inquires and information regarding the software offer for automatization and testing, please contact us at info@rio-system.com or by telephone at +972-3-5349109.